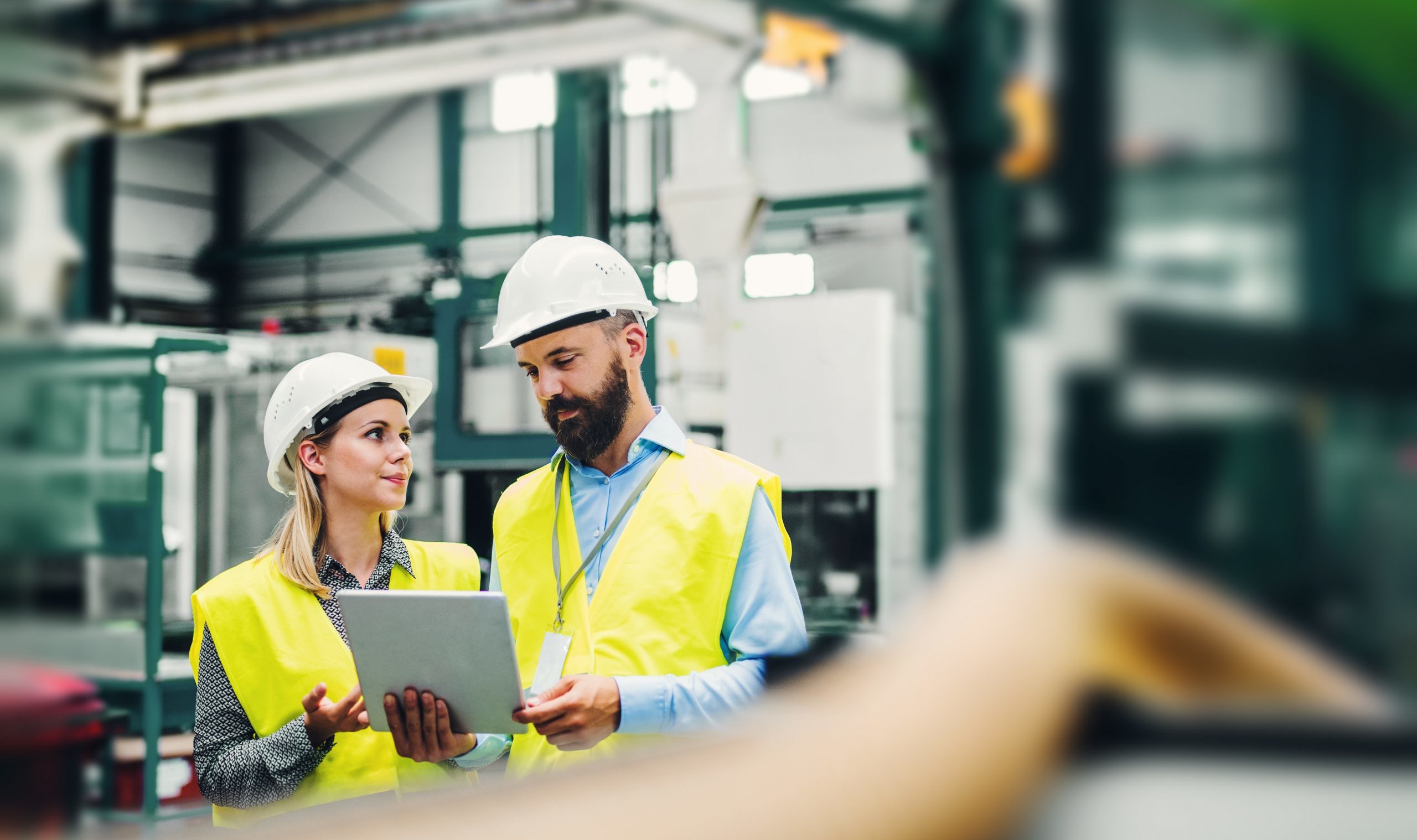
Minimize Risks with Shift Handover
Tired of incomplete, hard-to-read paper log books? Automate your event logs and integrate them with your control system.
Minimize Risks and Maximize Operational Effectiveness by Improving Communication
Every day, multiple people in multiple locations use your facility’s automation systems. How do they share information about what events have occurred and how they have responded? No simple task. Control rooms are full of paper logbooks in which operators have recorded events and documented their responses. Page after page, book after book, filled with important knowledge – only useful if someone can find the right entry and decipher the handwriting. At an extreme, tragic events can result from missed communication. More common, are the general headaches around manual shift logs that can result in inefficient day-to-day operations. Unless carefully managed, data tends to get lost in the paper trail. Facilities see productivity eroded and profits drained through errors brought on by these painfully routine conditions:
- Poor shift change communication — Inadequate knowledge sharing at shift handover negatively affects safety, product quality, delivery, and throughput. Manually transferring information to the new shift personnel is error-prone, and important items can be easily misinterpreted, improperly prioritized, or simply missed.
- Confusion in assignments and accountability — In some facilities, operators cannot focus on the key activities because they are unsure of priorities. As a result, they often must react to situations rather than actively manage their responsibilities. At the end of a shift, the supervisor must ensure that scheduled tasks were completed, difficult at best when logbook entries are manual and inconsistent.
- Difficult-to-share knowledge — Operators often cannot find key historical information in a series of paper notebooks, used to keep track of essential information. In addition, this unsecured, hard-to-read, and unreliable format is nearly impossible to share across the plant or with different facilities. Further prolonging problem solving and increasing the risk, context is missing from operator observations and process equipment data.
Achieve Better Visibility and Improve Operations Performance
Imagine an ideal shift change where the incoming operator fully understands what happened in the previous shift. No looking for a hardcopy logbook, no digging through unrelated information, no tagging pages. A unique tool, InfoLog™ exists today with the convenience of a browser-based application that captures electronic records of operator activity.
Minimize Shift Handover Risk
Setting a consistent, compliant shift handover process leads to minimized risk and increased operator effectiveness. With InfoLog, incoming operators have insights into events and issues from the previous shift via a shift change dashboard, shift status reports, and summary reports. These tools streamline shift change meetings and assist in compliance with documented communication between shifts. With accurate documentation in place, everyone can be confident tasks are not lost in the shift transition.
Drive Operator Action through Improved Task Management
Supervisors can use InfoLog to set and manage priorities by assigning tasks to an individual user or to a group. At login each operator is presented with a list of tasks, or “pre-flight” checklist, for the shift. The operator has a simple graphical interface that clearly presents priorities, offering greater visibility to the tasks that need to be done. Tasks do not go unattended and are recorded in the electronic paper trail. Operators act with the confidence that they are completing the correct tasks.
In addition to pre-defined task lists, personnel can generate ad-hoc tasks based on production asset health. When the list is integrated with repair work and order generation, plant operation is smoother because there is a stronger link between operations and maintenance departments.
Accelerate Decision-Making with Collaboration and Shared Knowledge
Because InfoLog presents an electronic historical record, operators have a plant-wide knowledge base, searchable across multiple logbooks. With that capability, similar past issues can be reviewed and current issues are quickly resolved. For ease of access, InfoLog consolidates information onto a single screen and offers easy-to-add meta-data so that operators have the context needed to resolve issues. Searches are productive because the information has embedded data structure and time stamps. When integrated with a distributed control system (DCS), such as the DeltaV system, information from InfoLog is viewed within the context of current process events — delivering greater visibility to critical production alarms and events, including process deviations. Operators can collaborate across shifts, plant areas, or facilities to solve problems faster. Armed with easily accessible key information and historical knowledge, operators and supervisors can react to issues more quickly and accurately.
Contact Informetric Systems for Efficiencies that Come with Knowledge
When you implement InfoLog with your automation system, you realize how important accessible, consistent knowledge is to operational success. We look forward to working with you and your organization to equip personnel with focused information — current and historical — to develop and maintain highly efficient and safe operations.